Enduction et insolation
Enduction et insolation des écrans sérigraphiques sont essentielles pour garantir une impression de qualité. L’enduction consiste à appliquer une couche uniforme de photopolymère sur la maille de l’écran : sans bulles ni irrégularités, l’émulsion doit être parfaitement lisse pour permettre un durcissement homogène. Ensuite, lors de l’insolation, l’écran enduit est exposé aux UV à travers un film positif ; les zones éclairées durcissent, et les parties protégées par le motif restent solubles pour être éliminées au développement. Un contrôle précis du temps d’insolation, adapté à l’épaisseur d’émulsion et au type de maille, est indispensable pour des résultats nets et durables.
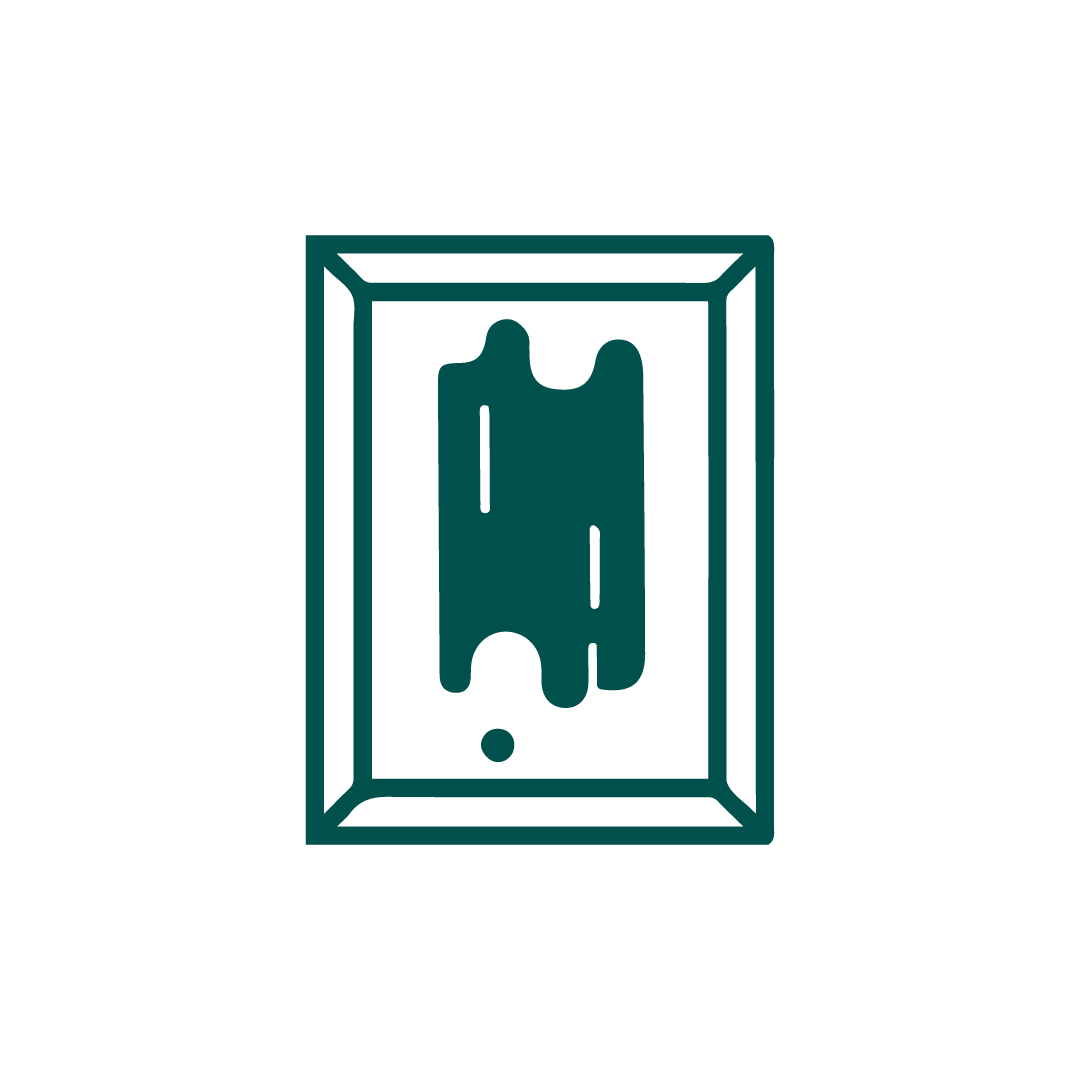
Détails prestations
Enduction : uniformité de la couche d'émulsion
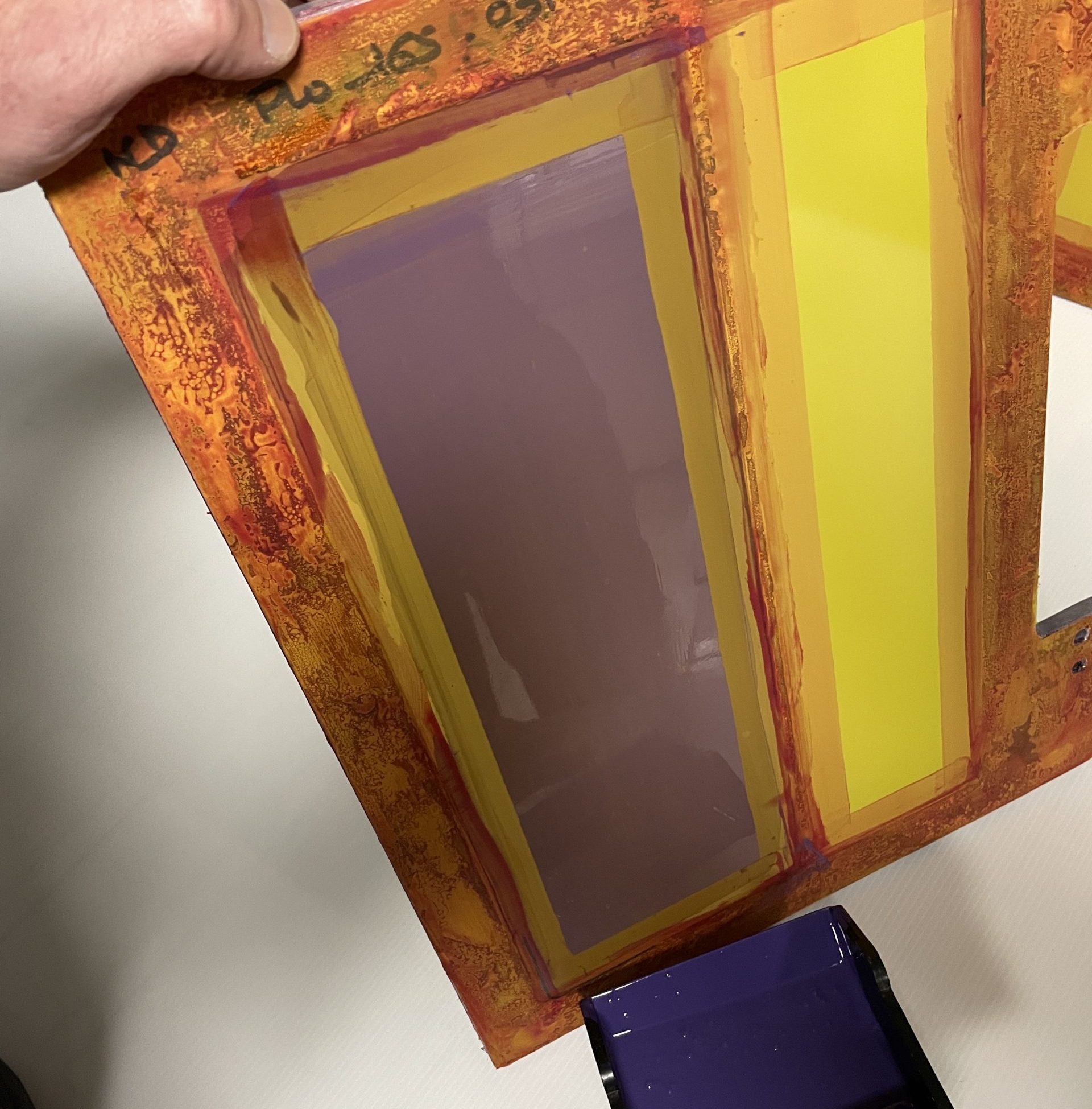
Une enduction correcte assure une application uniforme de l'émulsion sur l'écran sérigraphique, ce qui est crucial pour obtenir des impressions précises et de haute qualité sans zones inégales ou manquantes. Une bonne enduction permet de créer des bords nets et bien définis sur le pochoir, ce qui améliore la netteté et la clarté des détails fins dans l'image imprimée.L'émulsion contribue à la durabilité de l'écran sérigraphique, permettant des tirages plus longs sans dégradation rapide de la qualité d'impression.
Insolation : développement précis de l'image
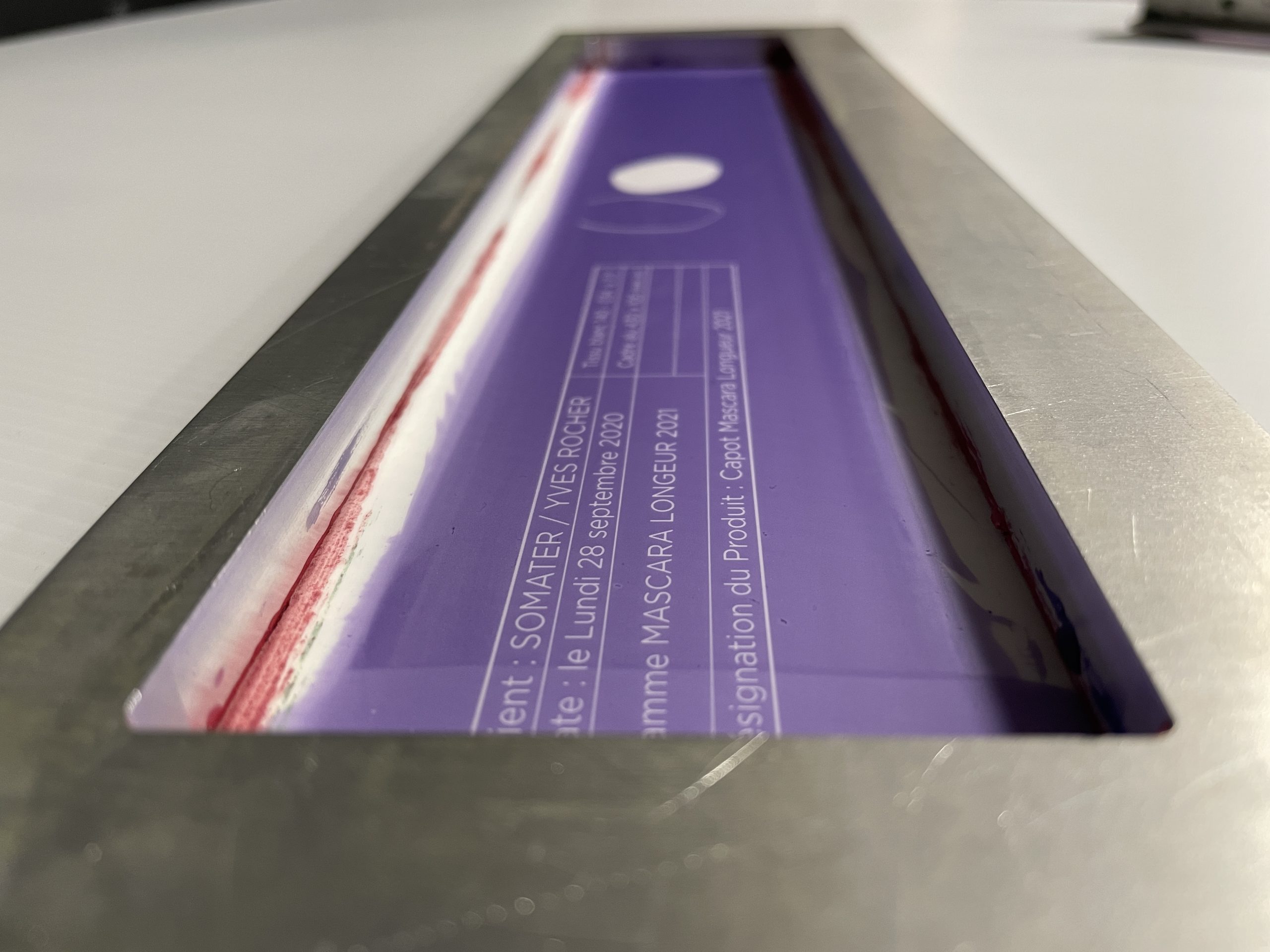
Une insolation correcte garantit que l'image sur l'écran sérigraphique est exposée de manière précise, avec des zones de lumière et d'ombre bien définies, ce qui est crucial pour des impressions nettes et précises. En contrôlant l'exposition à la lumièe, une insolation adéquate minimise les risques de sous-exposition ou de surexposition, évitant ainsi les défauts d'impression tels que les images floues, les détails manquants ou les résidus d'émulsion non durcis.